Your cart is currently empty!
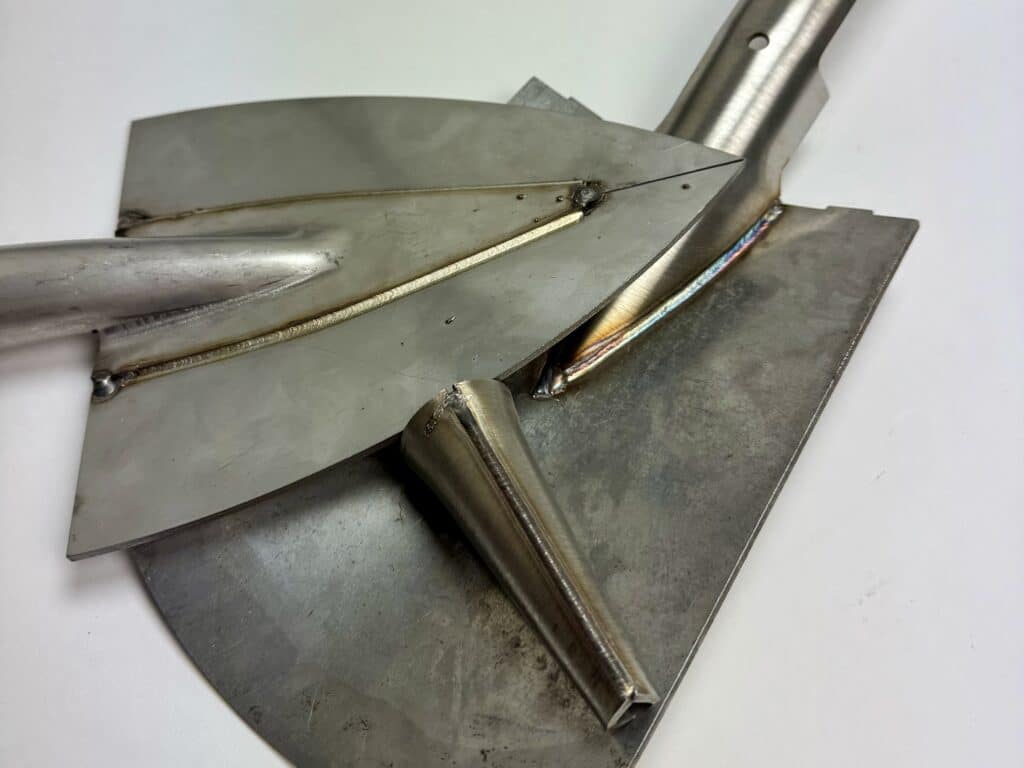
Traditional Welding Methods versus Laser Welding
At Sneeboer, we are always looking for ways to improve our production processes and reduce our carbon footprint. One of the key areas in which we have made significant progress recently is the welding process. Although traditional welding methods such as MIG/MAG and electrode welding have been used successfully for decades, the emergence of laser welding offers unparalleled advantages in terms of speed, precision and durability. In this article, we compare these welding methods and show why laser welding is the future for sustainable manufacturing at Sneeboer.
Traditional Welding Methods: MIG/MAG and Electrode Welding
MIG (Metal Inert Gas) and MAG (Metal Active Gas) welding have been reliable choices in metalworking for many years. These methods use a continuous wire as an electrode, combined with a shielding gas that protects the weld pool from oxidation. Electrode welding, also known as coated-electrode arc welding, uses a rod electrode that melts and forms a protective slag during welding.
While these methods are known for their versatility and relatively easy learning process, there are also limitations. The welding speed is limited, and the quality of the weld can vary depending on the skills of the welder. Moreover, the final product often requires extensive post-processing, such as slag and spatter removal, to achieve a smooth and aesthetically pleasing finish.
The Benefits of Laser Welding
Laser welding offers numerous advantages that far surpass traditional welding methods. This technique uses a concentrated beam of light to melt and join materials, resulting in an extremely precise and strong weld. Laser welding is particularly suitable for thin materials and precision work.
- Durability: One of the biggest advantages of laser welding is its durability. According to research by Fraunhofer ILT, laser welding is one of the most energy-efficient welding methods currently available. The process requires less energy than traditional methods and is faster, resulting in a significant reduction in CO2 emissions and a smaller carbon footprint.
- Less Post-processing: Laser welding produces a near-perfect weld seam, drastically reducing the need for post-processing. This not only saves time and costs, but also minimises the use of additional materials and tools, contributing to a more sustainable production process.
- Fast learning curve: Another great advantage of laser welding is the simplicity of the learning process. With the right training, new welders can lay down high-quality, consistent welds within just one day. This enables Sneeboer to train new welders quickly, which increases our production capacity and helps us meet growing demand.
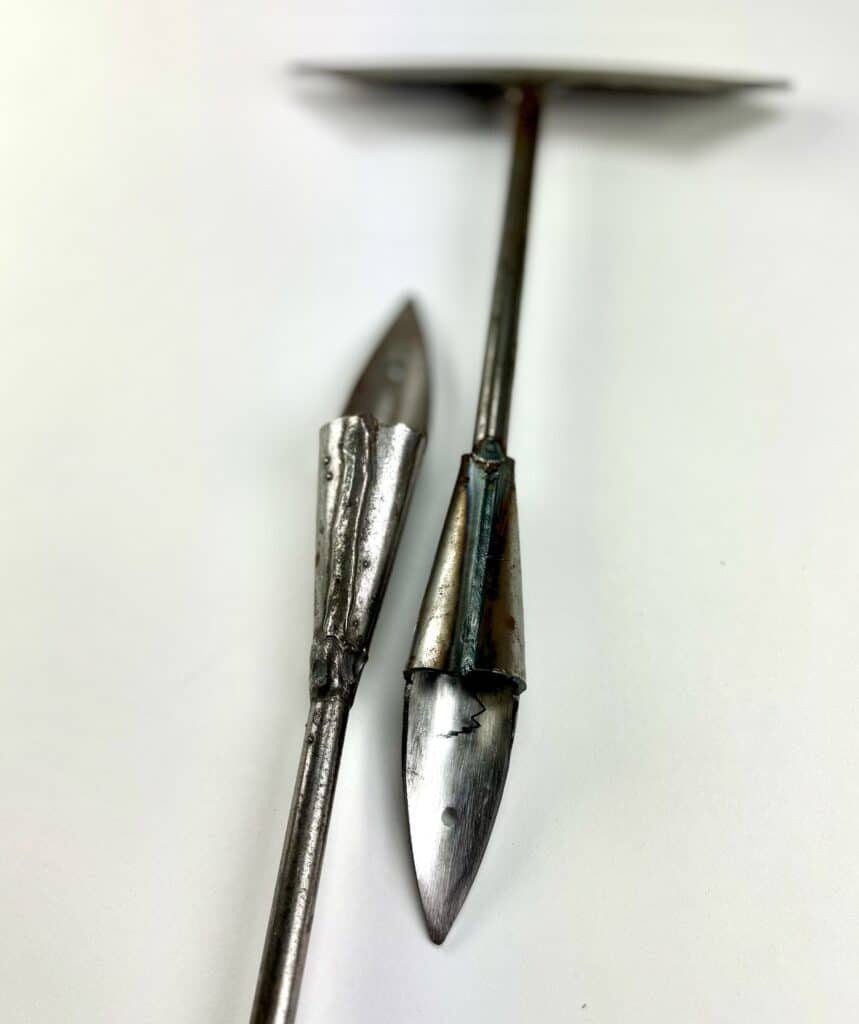
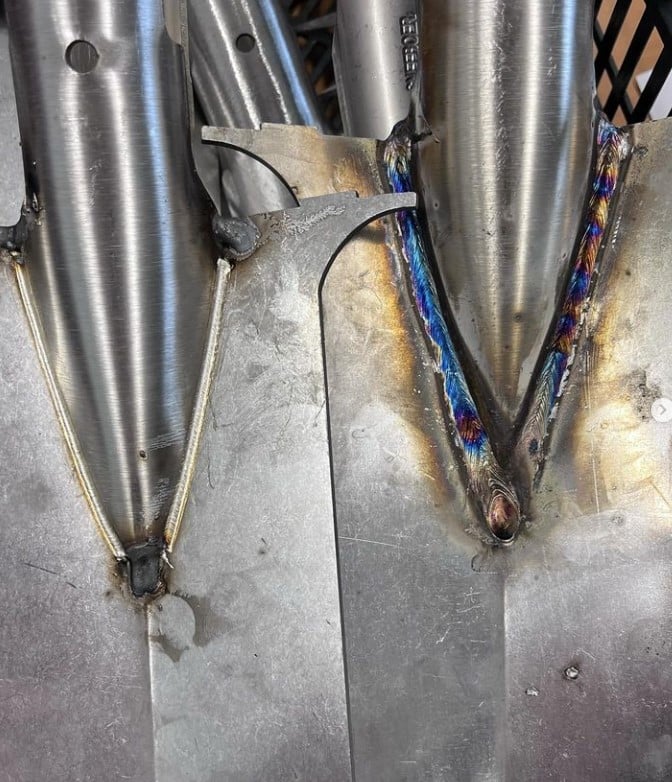
Innovation at Sneeboer since 1913
At Sneeboer, innovation is in our DNA. Since our establishment in 1913, we have consistently pushed the boundaries of technology and craftsmanship to create high-quality tools and products that are appreciated worldwide. The introduction of laser welding into our manufacturing processes is another step forward in our ongoing journey of innovation and sustainability. It is a perfect example of how we at Sneeboer always strive for improvement and perfection in everything we do.
At Sneeboer, we continue to look for innovative ways to optimise our production processes and reduce our impact on the environment. Switching to laser welding gives us the opportunity to work more sustainably by reducing energy consumption, minimising the need for rework and reducing training time for new welders. By investing in laser welding technology, we not only increase our production efficiency, but also reinforce our commitment to sustainability. We believe laser welding is the future of sustainable metalworking, and we are proud to integrate this advanced technology into our manufacturing processes at Sneeboer.